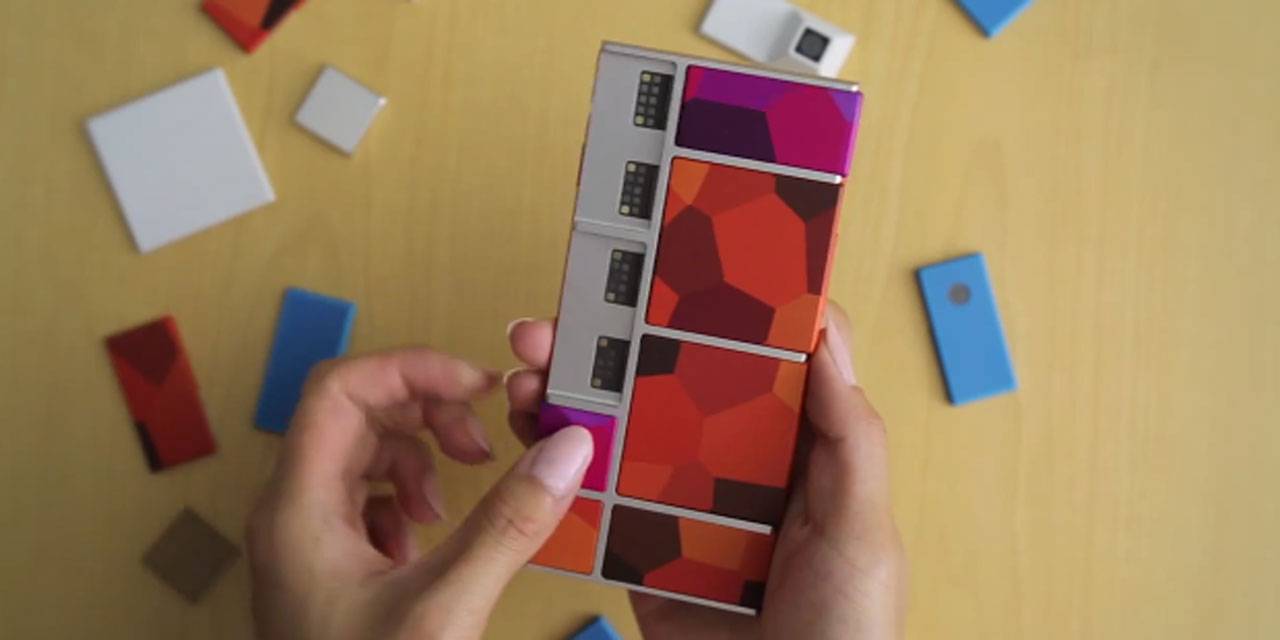
Project Ara is so revolutionary that it might not only change the way we make, buy, and use smartphones. According to 3D printing startup 3D Systems, it is already revolutionizing the very 3D printing process used to make it.
3D Systems has had the honor of being Google’s partner in this monumental endeavor but it isn’t all fame and glory. The modular smartphone project has very unconventional requirements. But more than that, it has required the use of 3D printing even when the time comes to mass produce the modules for public consumption and purchase. In order to meet those requirements, 3D Systems had to resort to no less unconventional methods and materials.
Most 3D printers today employ a reciprocating platform mechanism that times the motion of the platform that holds the object to be printed as well as the printer head. This, however, causes variance in speeds causing a longer printing time. Project Ara requires massive amounts done in a small amount of time, and so 3D Systems employed instead what it calls a racetrack architecture. Here, module shells move continuously, like in a racetrack, but there are also off ramps where final steps take place. The company has also partnered with Carnegie Mellon University (CMU) in order to find better and stronger materials as well as researching conductive inks for the more technical components.
The changes made in the 3D printing system might very well help make Project Ara a reality by its 2015 deadline. However, one question now is whether these innovations, which aren’t that common in the 3D printing world, can be replicated by other printers and companies. While it is good that 3D Systems was able to come up with this system, Project Ara’s future success, not just a smartphone but as an entire ecosystem, will rely on other players, big or small, being able to get into the game as well.
SOURCE: 3D Systems